Improve Reliability Of Carbon Monoxide Boiler Soot Blowers
Challenge

A large refining client needed to modify their carbon monoxide (CO) boiler soot blowers to improve the fluid cracking process (FCC) unit’s reliability. Parts for the soot blowers were becoming hard to source for the 40-year-old technology and timely updates to the equipment were needed to avoid damage to the boiler.
Solution
Valdes Architecture & Engineering’s plan included the replacement of the six upper soot blowers’ pneumatic motor drives with electric motor drives and a full replacement of the obsolete bottom three blowers with electric drives. The bottom blowers were designed to be fully retractable with isolation valves from the boiler. Valdes provided front-end loading (FEL) work that involved a preliminary stress review only. Upon FEL approval, Valdes completed the mechanical, piping, structural and instrumentation and electrical (I&E) design needed to connect/install the three new soot blowers and reconnect the other existing six soot blowers attached to the boiler. Pipe stress analysis was performed using Caesar II and CADWorx-3D Modeling was used to verify the design.
Impact
Valdes provided our client with improved reliability of the system and an increase to the efficiency of the blowers, as well as a design that allowed for ease of access for routine maintenance.
Services

Structural

Mechanical

Instrumentation & Controls

Pipe Stress Analysis
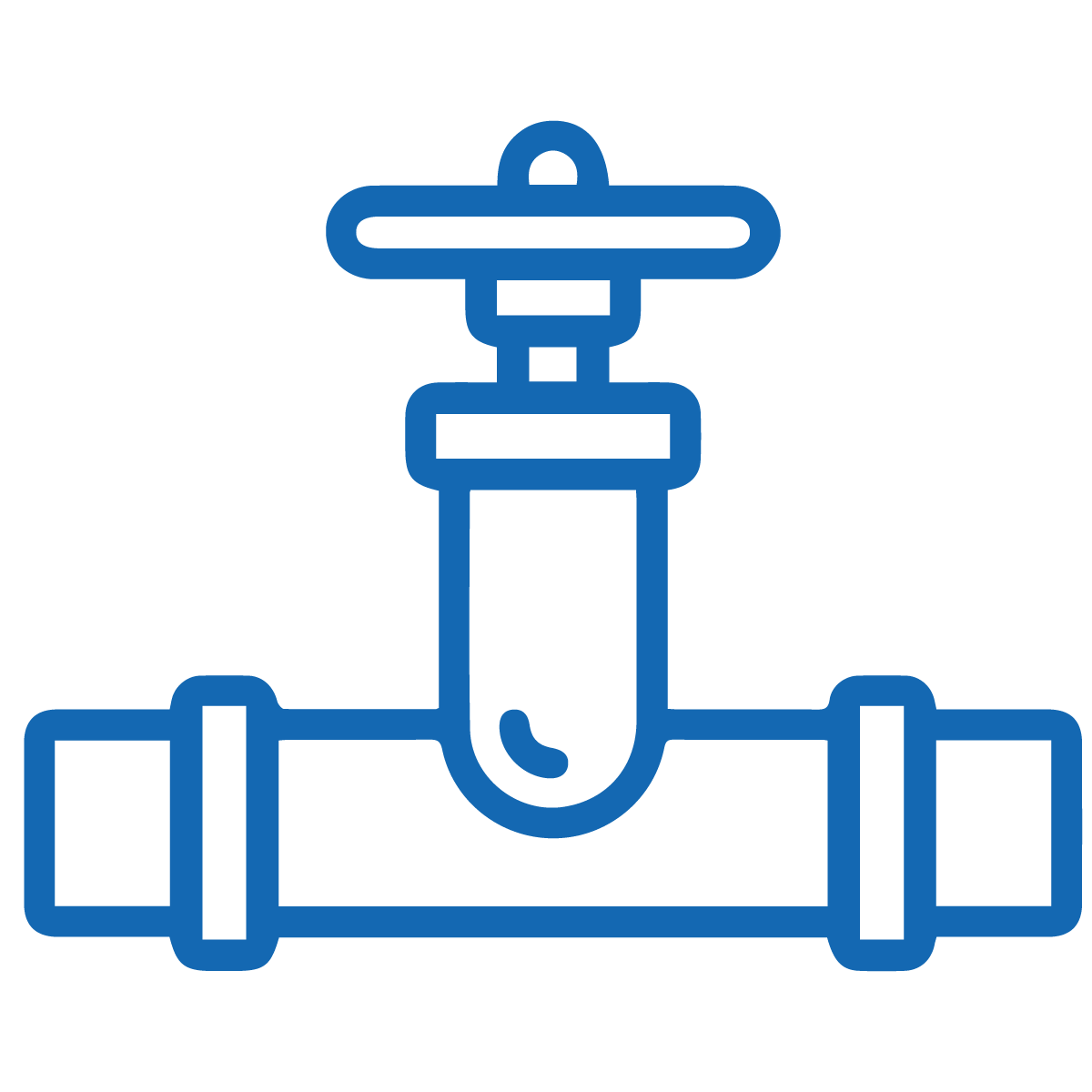
Piping & Plant Layout

Laser Scanning & Surveying